
Roll Inspection
PERFECTING THE INSPECTION PROCESS FOR DEFECT-FREE ROLLS WITH ROBUST AND PROVEN TECHNOLOGY
Sarclad takes pride in providing the best technology and products to our customers. The Rollscan is our roll inspection product providing the inspection data you need to manage the longevity, safety and quality of your rolls fleet.
Rollscans are prevalent across the global steel industry in both hot and cold rolling mills, providing inspection data to guide the grinding process across both work and back up rolls. It identifies the depth and location of any defects in the roll above the set threshold.
It enables data driven grinding, allowing the grind depth to be set the level necessary and avoiding the removal of any unnecessary wear of the roll. Our customers find that the payback on a rollscan investment is typically less than 1 year, due to longer longevity of roll life, improved rolling quality and less unplanned maintenance due to roll issues. Rollscans are increasingly popular in the aluminium rolling industry also, for flat product applications such as Automotive.
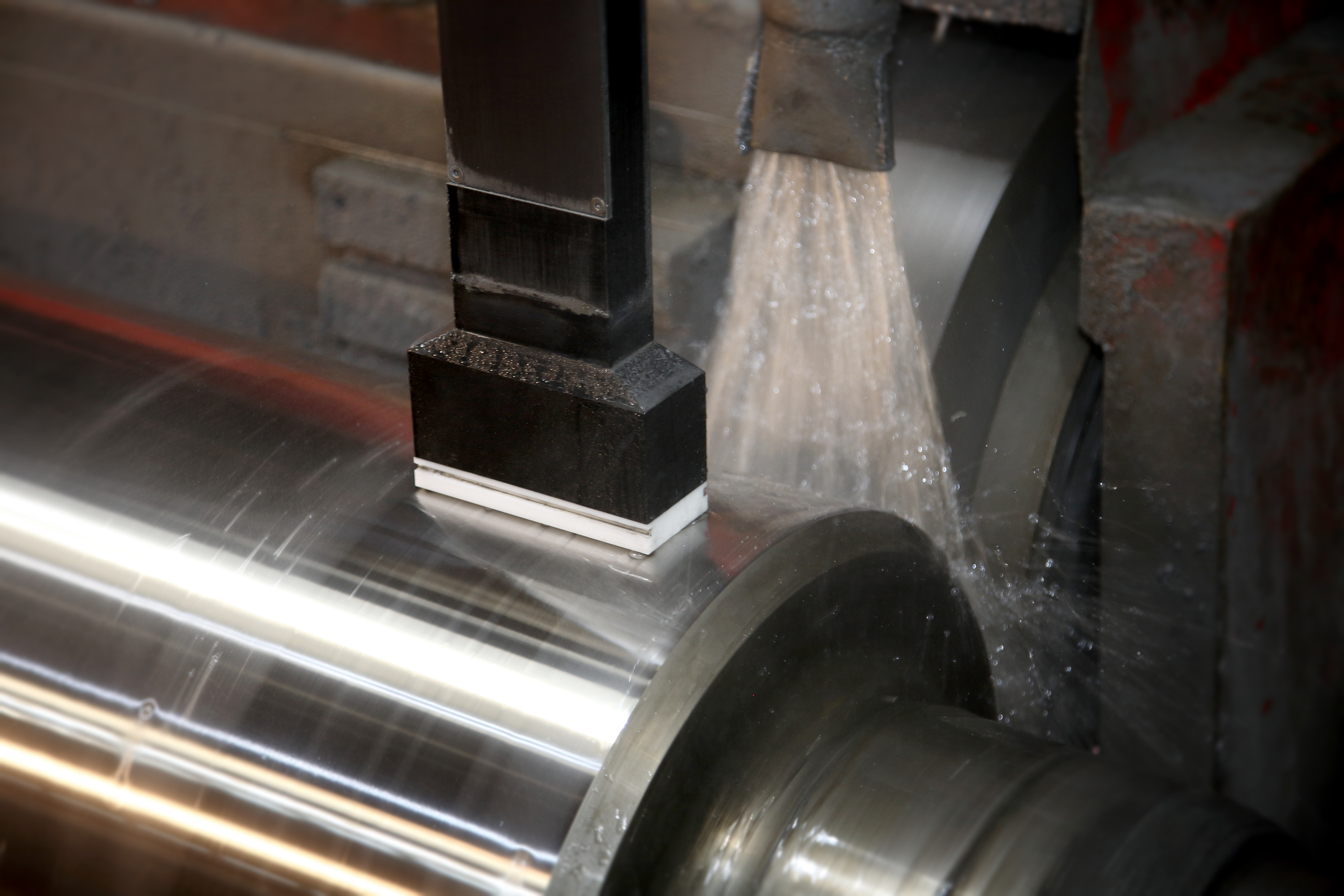
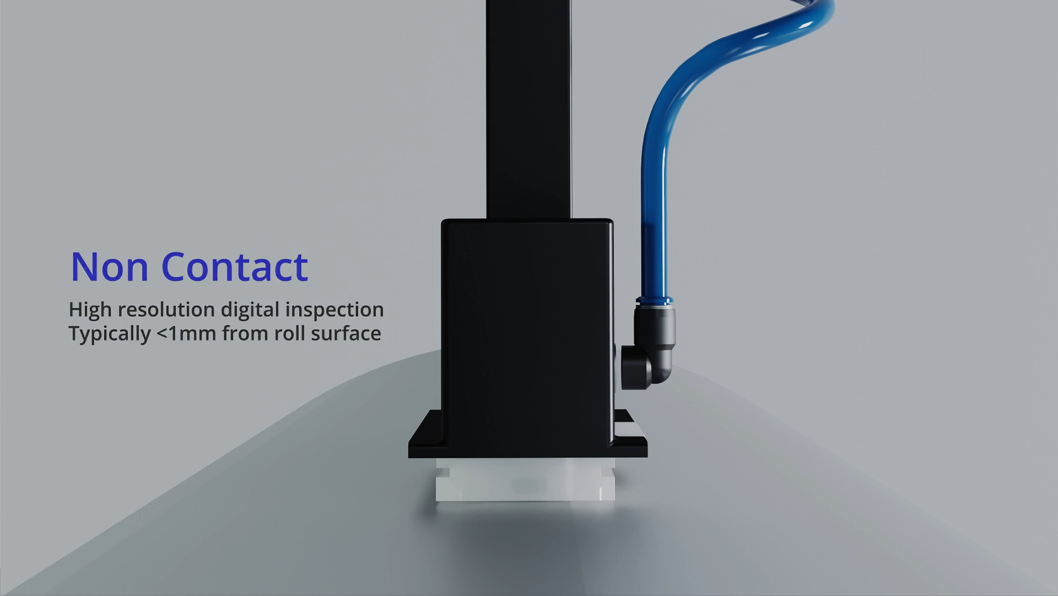
The Rollscan unit may be operated as a stand-alone unit or integrated with the grinder itself. It offers a single easy to operate probe head that can be customised to provide the roll inspection required. This varies from surface only inspection requirement, provided by eddy current technology, through to complete roll coverage with ultrasonic inspection technologies added, enabling just below the surface inspection and deep into the core inspection.
Our engineers developed Rollscan to ensure the quality from the grinder is consistently perfected and maintained.
Benefits of Rollscan
-
Enables data driven control of roll grinding process
-
Effective on cast and forged rolls
-
Extremely robust and simple to use
-
Effective on work and back up rolls
-
Supports safe operating practice (identifies suspect rolls)
-
Payback typically less than 1 year
-
Excellent service and spares support globally
-
Surface/ sub surface and core inspection available
It is critical our customers can trust our products and know they will work accurately and reliably. Sarclad provides 12 month warranty protection from final acceptance and a commitment to support the purchased unit with replacement parts and service for a minimum period of 10 years. Rollscan units are well known for their longevity in the industry
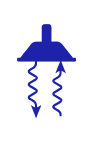
Surface Inspection (Eddy Current)
If you are only concerned about surface cracks and bruises on your rolls, the Eddy current only Rollscan, will the right fit for you. The head features 8 powerful eddy current probes. When the probes probe passes over a surface breaking crack or bruise on the roll surface, the induced eddy currents are disrupted. This disruption is then recorded, interpreted, and displayed by the Sarclad Rollscan system as shown in the rollscan brochure. This version is not designed to detect sub-surface issues.
Sub Surface Inspection (Ultrasonic inspection)
For customers also seeking beneath the surface inspection, high frequency ultrasonic probe(s) can be added to the head to detect internal defects. The ultrasonic probe transmits a sound wave and when a defect is present receives a reflection of that sound wave (an echo) which is then quantified compared to the original, recorded and displayed by the Sarclad Rollscan system.
Subsurface Flaws Typically Detected:
Areas of Porosity
Non-Metallic Inclusions
Internal Cracks
Interface/ Bond Separation
Detection and scanning of the above enables removal of suspect rolls for further investigation and avoidance of catastrophic roll failure.
There are two types of Ultrasonic Inspection that can be added to the head
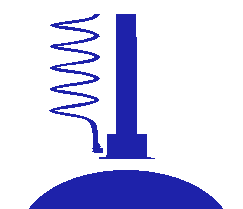
Core Sub Surface Inspection (Compression Wave)
The compression wave ultrasonic probe transmits a sound wave and when a defect is present receives a reflection of that sound wave (an echo) which is then quantified compared to the original, recorded and displayed by the Sarclad Rollscan system. This technology can be used to inspect over 100mm into the core of the roll.
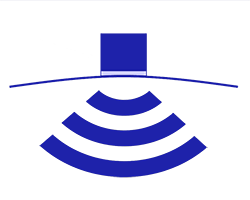
Just Beneath the Surface Inspection
An ultrasonic technology called surface wave or creep wave can alse be added to the probe head to specifically assess for defects that may be just below the surface
Surface wave works by angling the ultrasonic beam obliquely at the roll surface. Once this angle of incidence is above a critical point, the beam no longer penetrates towards the roll centre but instead travels around the roll circumference allowing detection of defects immediately below the surface.
See brochure for more information